Transparency in our audit process allows auditors to properly review wages, benefits, insurance and working hours to ensure the factory is following legal and A&F Co. Vendor Code of Conduct requirements.
Our Strategy
Supplier Assessments
Through the A&F Co. social audit program, facilities throughout our supply chain are assessed to ensure labor and social commitments are adhered to by all parties involved. A&F Co. partners closely with our vendors to assess and remedy findings found during the audit. For more information see Supplier Assessment.
Worker Wages
Ensuring workers receive wages that conform with minimum wages prescribed by local law is a priority to A&F Co. As a first step to understand how workers’ take-home wages in Bangladesh compared to legal minimum wage requirements, A&F Co., factories, and a third-party monitoring firm piloted a wage analysis exercise in 2019.
The analysis was performed through a desktop payroll review of the same 50 workers from July to December 2019. The purpose of the review was to:
- Confirm minimum wage is guaranteed and overtime rate meet legal standards
- Determine the average percentage workers are being paid above the legal minimum wage (excluding overtime)
- Verify legally mandated benefits and severance are guaranteed
As a result of the review, it was determined that nearly 70% of workers received take-home wages above the legally required minimum.
Our Progress
In 2023, the most common findings for the categories with the highest percentages were:
Working Hours
- Overtime hours not compliant with legal regulations
Wages and Benefits
- Social insurance provided
- Paid leave
The chart below shows the percentage of factories with findings of non-compliance in each category.
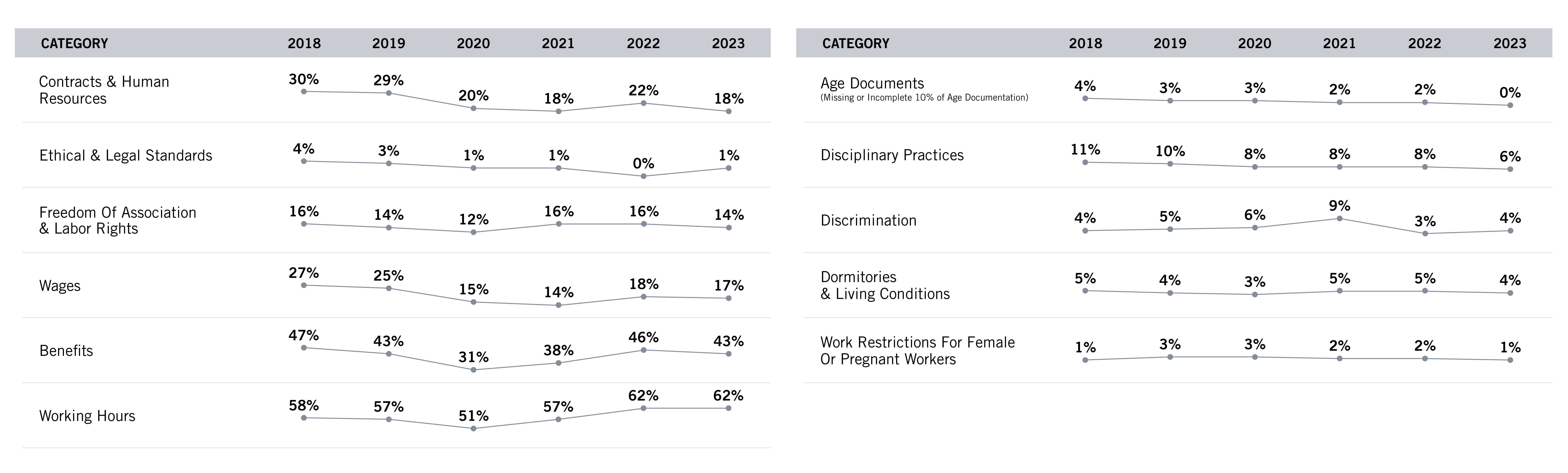
To help address these issues, A&F Co. partners with Better Work to strengthen the factories’ monitoring and management system, knowledge of legal requirement and sharing industry best practices. Factories in the Better Work program implement 15 to 25 training days (depending on the country). Based on the specific needs, each factory will develop their training plan under Better Work enterprise advisors’ guidance. In addition, Better Work will conduct 3 to 5 advisory visits to factories to develop an improvement plan and assist factories to correct the issues.